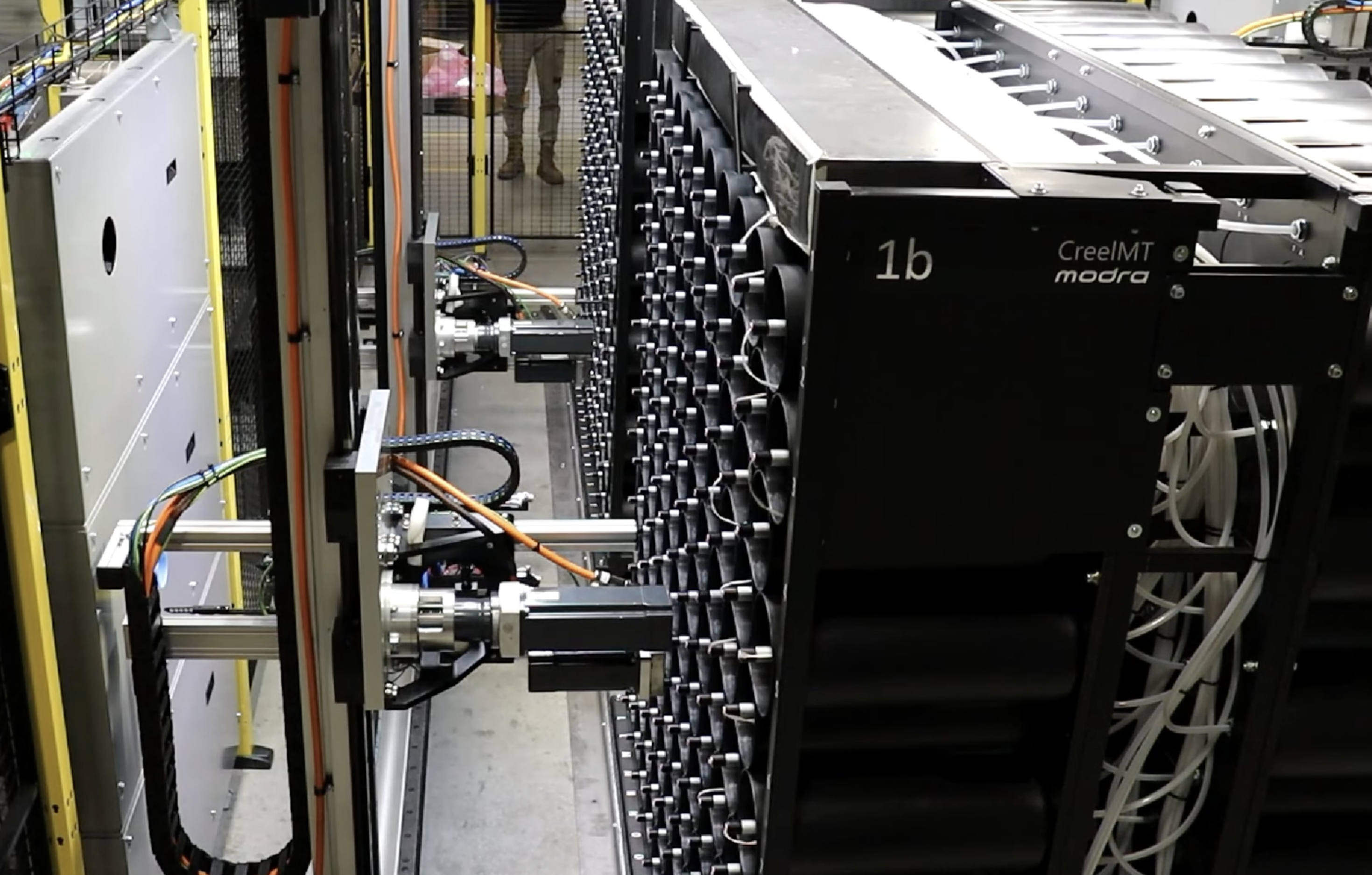
Do you have a tufting machine capable of variable yarn draw at each needle position? Do you want to do short product runs economically and efficiently? Do you want to expand your design options? It may not seem obvious, but a creel automation system could be exactly what you need.
Challenges with traditional fixed creels
The traditional fixed creel works best with big packages of yarn, supplying a tufting machine with equal yarn length at each needle. However, if you have a tufting machine that is capable of variable yarn length at each needle – like a ColorPoint or an Infinity or an iTuft for example, it can be challenging to work efficiently with a traditional fixed creel.
There are several ways manufacturers deal with this challenge. One way is to ask designers to minimise the colours per position. For example, try to limit to two pile heights per colour or even just two pile heights per pattern.
Another approach is to use the packages of yarn without worrying too much about what is being consumed by the needle. You can add more yarn and splice it in the creel as it runs out or switch positions and try to load balance while operating the tufting machine. However, this method requires a lot of manual labour during tufting and is probably not an ideal or acceptable solution.
You could also ask your supplier to wind to the maximum length. The idea of winding to the maximum length is so that at least one yarn or small group of yarns will run out together. That signals the end of the run, and everything trails out behind that, with the remnant material remaining on the package. However, this method locks you into deciding precisely how much yarn you need and when you will receive it from the supplier, which means you lose flexibility in defining when you want to pull the product from your master stock.
Another option might be to wind to the maximum length yourself, or you could wind to the maximum length per colour to get closer to what the tufting machinery is consuming for each colour. You could also divide the colours into groups and have several maximum lengths.
Another solution would be to wind every needle position to the correct length, then mark those packages with their creel location and manually place the packages.
These solutions are all ok, but there is a better way.
The automated creel solution
It is already possible to wind every needle position to the correct length, but to be a truly automated solution, there’s a missing step – you still need to get the wound package to the correct creel pin location. This is where CreelMT comes in. Using a combination of robotics, software, precision winders and mobile creel trolleys, the CreelMT winds the required yarn length for each needle position and places the wound package of yarn in the mobile creel trolley in the correct position. Imagine - your tufting machine is being fed by a set of mobile creel trolleys that have been prepared by CreelMT, there is another set of prepared creel trolleys ready to be beam spliced to your tufting machine when the current job is finished, all while the CreelMT is busy preparing another set of creel trolleys. A complete, continuous cycle with minimal down-time for your tufting machine. Think about what this would do to your OEE. Think about how quickly you could complete a changeover from one run to the next. Consider what this could do to your profitable run length, your stock holdings, and your ability to respond to customer requests by reducing your run length.
Considering all the above, why wouldn’t you consider a creel automation machine?
Review the CreelMT here.
SUBSCRIBE TO MODRA TECHNOLOGY NEWS >