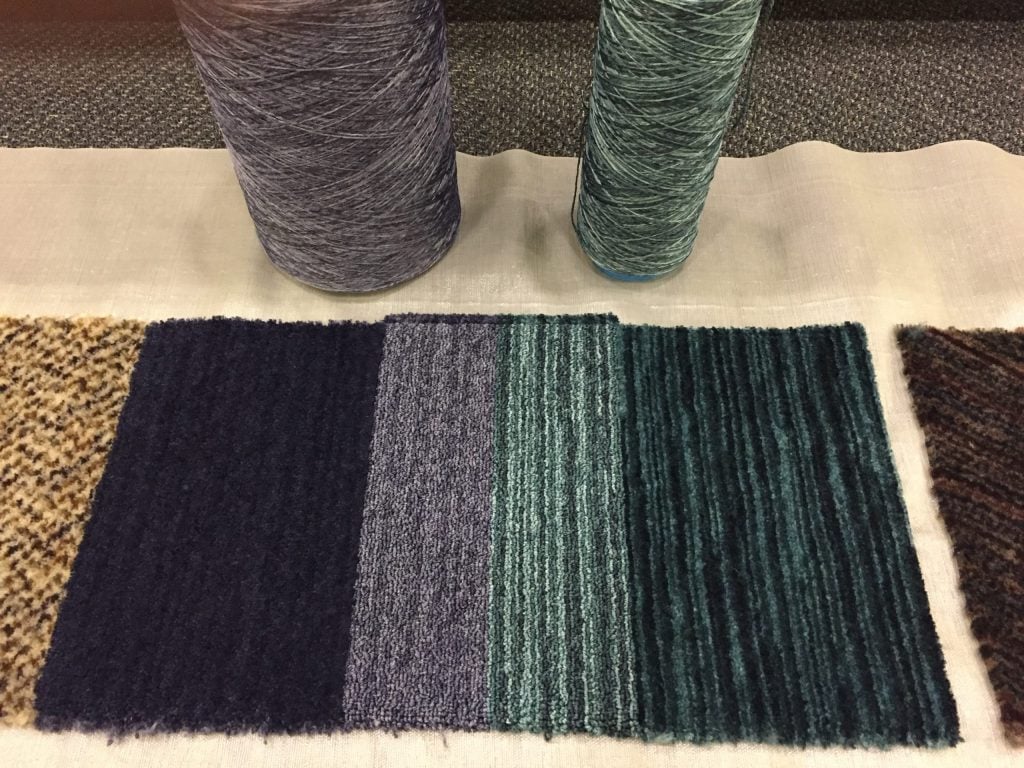
A quality control scenario*
A long-standing partnership at risk
A few weeks later, the carpet manufacturer reached out with a severe problem. The yarn had caused defects in their carpet production, impacting a major project. It wasn’t just about the immediate issue, it was about the long-term damage this could do to the relationship. A $400,000 penalty was swiftly imposed under the terms of their long-term supply agreement. Alongside that, the cost of replacing the yarn and the lost time put immense strain on the yarn manufacturer. The hit to their reputation was even more damaging, not just with the carpet company but across the industry.
It was a turning point for the yarn manufacturer when their reliability and credibility were hanging by a thread. But instead of giving up, they decided to learn from this painful experience and find a way to prevent it from happening again. They identified that they needed an additional step in their process which verified each batch. That’s when they turned to Modra Technology’s Mtuft Mini.
A turning point: learning from mistakes
The Mtuft Mini provided a precise, fast way to test each batch of yarn, ensuring quality and consistency before any yarn left the factory. Spotting a defect in yarn is very difficult but a defect in carpet is much easier. With no room for future mistakes, the yarn manufacturer integrated the Mtuft Mini into their production process. A sample of yarn from each batch was now turned into a piece of carpet, made on the Mtuft Mini and thereby checked with the details only a finished carpet can provide.
Soon, confidence began to return within the company. The next delivery to the carpet manufacturer went through without a hitch, and the carpets produced from this batch were flawless. Trust, though damaged, began to rebuild. The yarn manufacturer’s long-standing partnership was still intact, thanks to their proactive steps to ensure future reliability.
Rebuilding trust, one batch at a time
The investment in the Mtuft Mini solved an immediate problem and restored the manufacturer’s reputation for quality and reliability. The carpet manufacturer was reassured, and other industry partners noticed how the company had used cutting-edge technology to rise from a serious challenge.
Ultimately, the yarn manufacturer emerged stronger, more confident, and equipped with the tools to ensure that such an oversight would never happen again. The Mtuft Mini had become a critical part of their success, not just in production but in maintaining the long-term relationships that were the backbone of their business.
* This is a scenario based on the lived experience of a carpet yarn manufacturer.
SUBSCRIBE TO MODRA TECHNOLOGY NEWS >