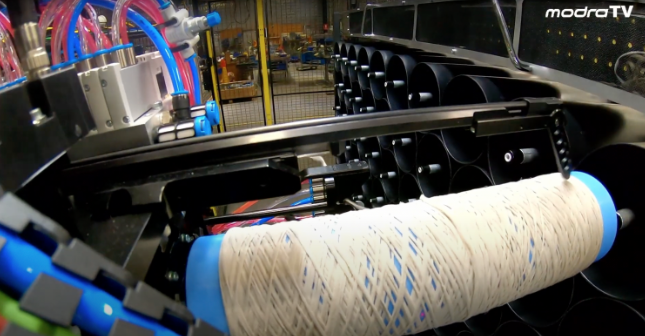
In the continuing focus on OEE, “Process Defects” is the most curious of the six big losses for carpet manufacture.
The impact of process defects can be devastating
In a normal consumer product manufacturing process, process defects can occur on a semi-regular basis, with individual products being removed from the production line or even replaced for the customer if they make it through the process. However, for carpet manufacturers, a process defect can affect the entire run of carpet and often means the stopping of production and destruction of the carpet produced. Waste or resources including material and time can be enormous at this point.
Tools like Six Sigma, ISO 9000, Total Quality Management, and the 5 ‘S’ Methodology are some of the most powerful and effective tools available in the market that manufacturers can use to reduce defects in their production process. However, most of them are not applicable to carpet manufacturing.
For example, “inspection” and “maintaining strict quality control” sound great but help little with the human error side of carpet production. Making simple "product designs" puts too many restrictions on production innovation which is the crux of the industry. Having "flexibility in production" sounds ideal but it is hard to apply to a tufting machine taking "preventative actions" such as replacing obsolete equipment, as well as making sure that all operating machinery is functioning perfectly. This all sounds great but how much time (and money) do you put into it?
How to prevent process defects in carpet manufacturing
The use of technology or “Smart Manufacturing” is perhaps the only practical recourse for great gains in process defects for carpet manufacturing. In this case, the use of technology is not about detecting defects early but preventing them altogether.
- Examples of common reasons for process defects include incorrect equipment settings, operator or equipment handling errors and slight colour changes from one batch of yarn to the next.
- Incorrect creel set-up means a stop in production, a return to the set-up process (meaning much more time) and then wastage of the yarn itself.
- A robotic package handling system, which allows for a single operator to load the pattern data and creel map via a simple Excel spreadsheet can eliminate these mistakes as you are no longer relying on individuals to manually check and re-check the creel layout.
- A robotic package handling system, which allows for a single operator to load the pattern before the set-up process eliminates many of the process defects which often occur in a carpet manufacturing process.
This is where the CreelMT from Modra Technology come in - it is a robotic package handling system combined with precision winding and a mobile creeling system.
Watch the CreelMT in action here.
Contact the experts
Please get in touch should you wish to request a trial or if you have any questions.