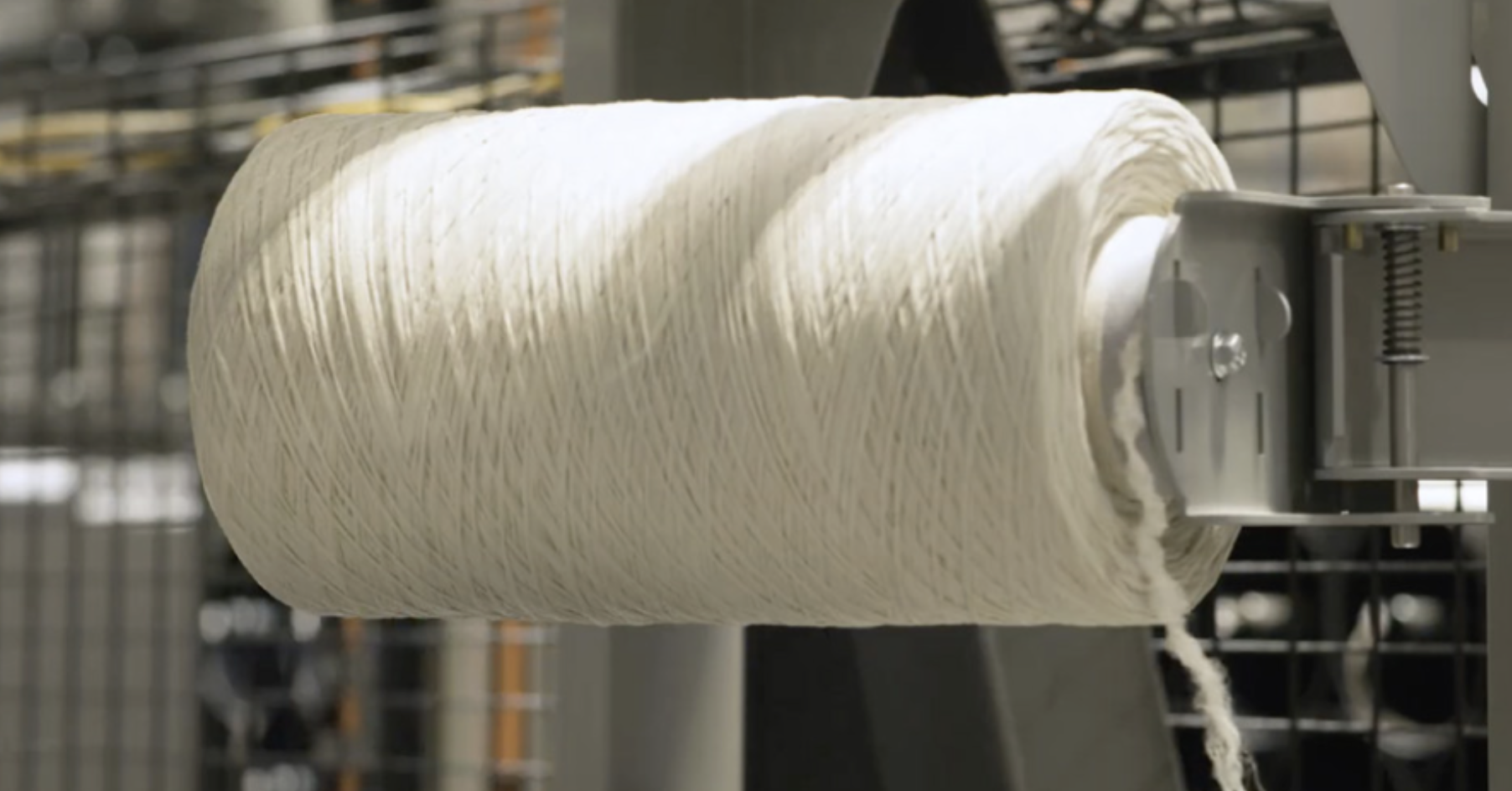
Overall Equipment Effectiveness (‘OEE’) is a measure of manufacturing productivity that considers three factors: availability, performance, and quality. “Idle time” and “downtime” are two factors that can have a negative impact on OEE.
Idle time refers to when a machine is not running but still consuming energy. This can happen when a machine is waiting for input, the operator has paused the machine, or during a changeover. Idle time reduces the availability of the machine and therefore lowers the OEE.
Downtime refers to brief pauses in production that occur for various reasons, such as clearing a jam, adjusting settings, or loading/unloading materials. While these stops may seem insignificant, they can add up and impact the performance of the machine, leading to reduced OEE.
A common downtime in the carpet industry can be caused by using re-wound yarn. To avoid wastage, yarn is often wound and rewound. Re-wound yarn will often have splices and knots which can result in weakness, causing the yarn to break and the tufting machine to stop. If this downtime happens often enough it can have a negative effect on the end quality of the carpet, the amount of labour needed to run the equipment (and therefore labour cost), the total time taken to complete a run (interrupting the schedule), and of course OEE. To improve OEE, it is essential to minimise idle time and downtime.
So how do you avoid the use of rewound yarn?
Wind to the specified length for a run. For every needle position the length of yarn required is known. To ensure there is enough yarn to complete the run, Modra’s CreelMT™ adds a small buffer of 2-5% of additional yarn per needle position. At the end of the run, the small amount of leftover yarn can simply be recycled, and the rewinding process can be avoided altogether.
Other benefits include:
- Doing away with the need to rewind, label and store packages of yarn means a significant labour saving.
- Avoiding the problem of mixing yarn batches can also have an impact on the quality of the finished carpet.
Many other benefits are associated with automatic package handling and precision winding, but reducing idle time and downtime are infrequently considered but important elements to increasing total OEE.
Modra’s CreelMT™ - an automated yarn creeling system - effectively reduces idle time and downtime. It does this by combining precision winding, robotic package handling and mobile creel trolleys.
Contact us today to learn all about CreelMT
The CreelMT is not only a solution to the setup process but it can help reduce lost time due to equipment failure and adjustment time. Please have a chat with us about all the different solutions that might help your business.
Contact Modra today >