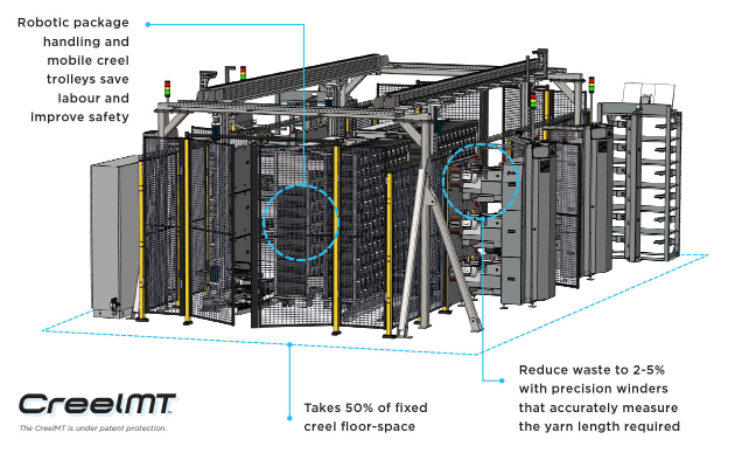
Make to Stock and Make to Order are two different production strategies used by businesses to manufacture and supply products.
Make to Stock (‘MTS’) is a production strategy in which products are manufactured in anticipation of customer demand, without specific orders. The manufacturer produces products based on forecasts and historical sales data. The goal is to have enough inventory to fulfil customer orders quickly, without experiencing stockouts or backorders. This is the principal production method for the carpet industry.
On the other hand, Make to Order (‘MTO’) is a production strategy in which products are manufactured only after receiving a customer's order. The manufacturer starts production only when an order is placed, and the product is tailored to the specific requirements of the customer. MTO is becoming the norm in many industries. It requires an efficient production process, one that includes automation and perhaps even the use of robotics – there are now 3.6 million industrial robots in the world as of 2022.
There are many advantages of MTO
- Customisation: MTO allows businesses to tailor products to meet the specific needs and preferences of individual customers, which can lead to higher customer satisfaction. Happy customers build customer loyalty and confidence, keeping them coming back for more.
- Reduced inventory costs: MTO allows businesses to avoid the cost of carrying excess inventory, as production is based on customer orders. As interest rates increase, the cost of carrying this stock increases.
- Reduced waste: MTO can reduce waste by producing only what is needed, as opposed to producing in bulk and potentially having excess inventory. Excess inventory in the carpet industry is common, and we see it time and time again with discounting required to reduce inventory of the finished product.
- Flexibility: MTO allows for smaller run sizes and the ability to quickly change the order of jobs on the production line in response to customer needs or other market conditions.
- Higher profit margins: MTO can result in higher profit margins, as customers are typically willing to pay more for customized products.
MTO often means smaller production runs, and perhaps one of the reasons why this is challenging to implement. After all, the time it takes to manually load a creel and splice in the yarn, often means short runs are not cost-effective or an efficient use of resources. So how can the time to creel and splice be reduced?
Automated Creeling
An automated, robotic package handling system, combined with beam splicing, will reduce the changeover time and increase productivity.
Modra’s CreelMT™ is an automated yarn creeling system, that along with the use of robotics, places precision wound yarn packages into a mobile creel trolley. The yarn in the mobile creel trolley is then beam spliced to the tufting machine. With CreelMT™, it is possible for a skilled operator to beam splice a full set of creel trolleys in less than one hour.
The use of Modra’s CreelMT™ makes MTO and small run sizes, along with increased productivity a reality.
Click here to view a recent discussion on the CreelMT™ and how it works to reach this goal.
It is then up to sales, ordering and scheduling to keep up with the new method of production. With higher profits and happier customers up for the taking, MTO seems the way to go.
Contact Modra today to learn more about CreelMT™